Ideation & Prototyping Week 13
Research for Design #4 Prototyping & Reflections
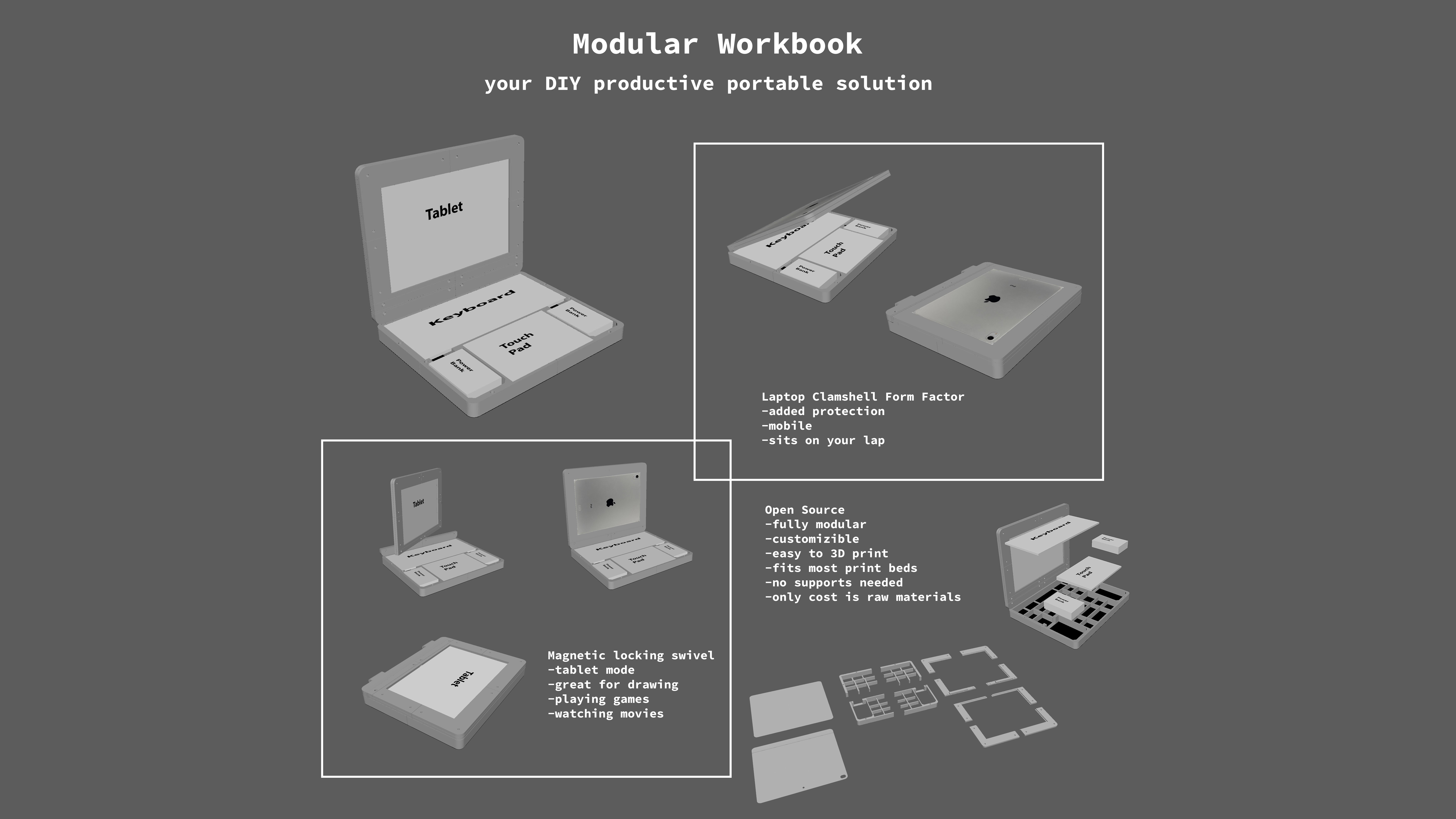
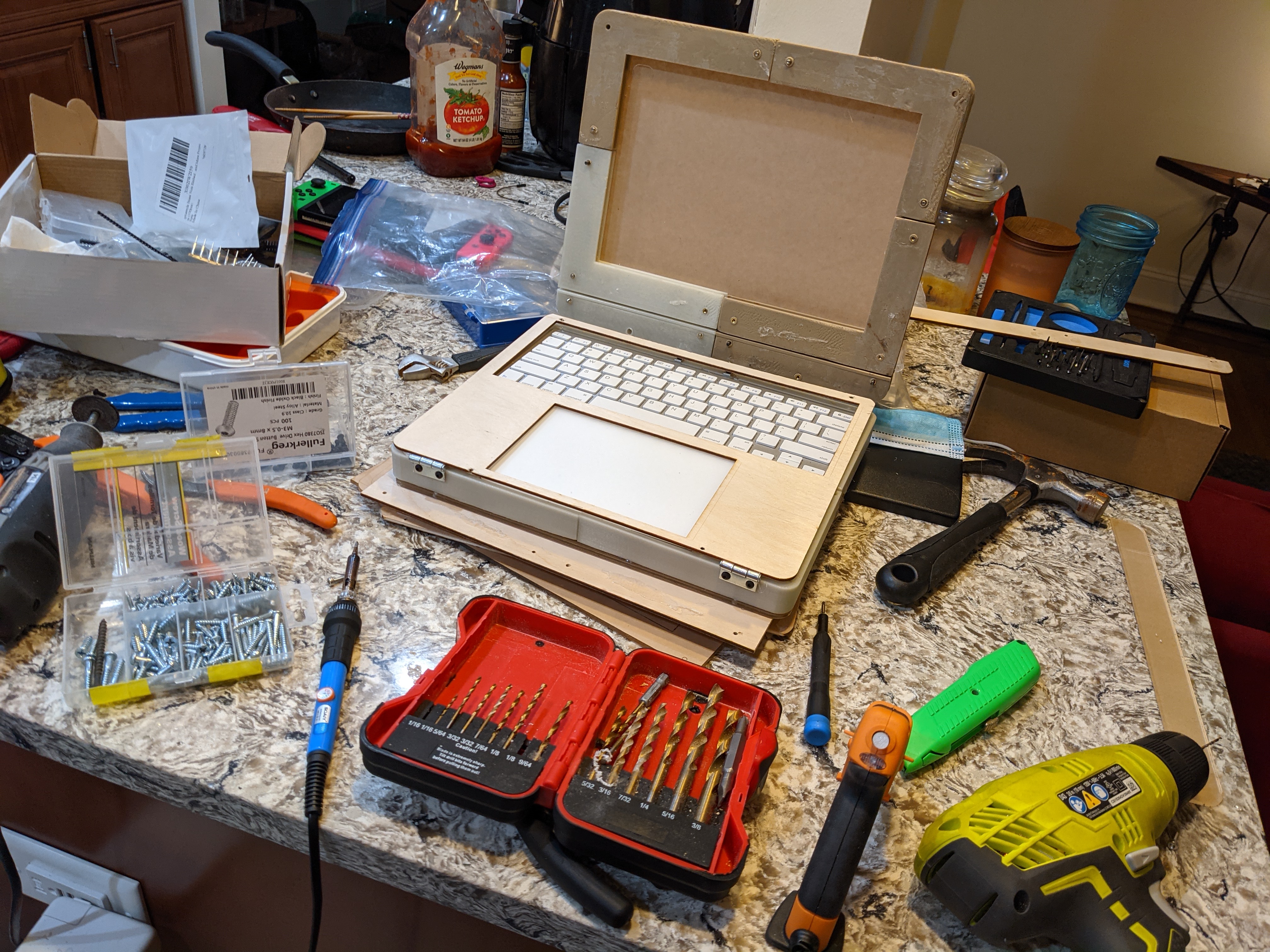
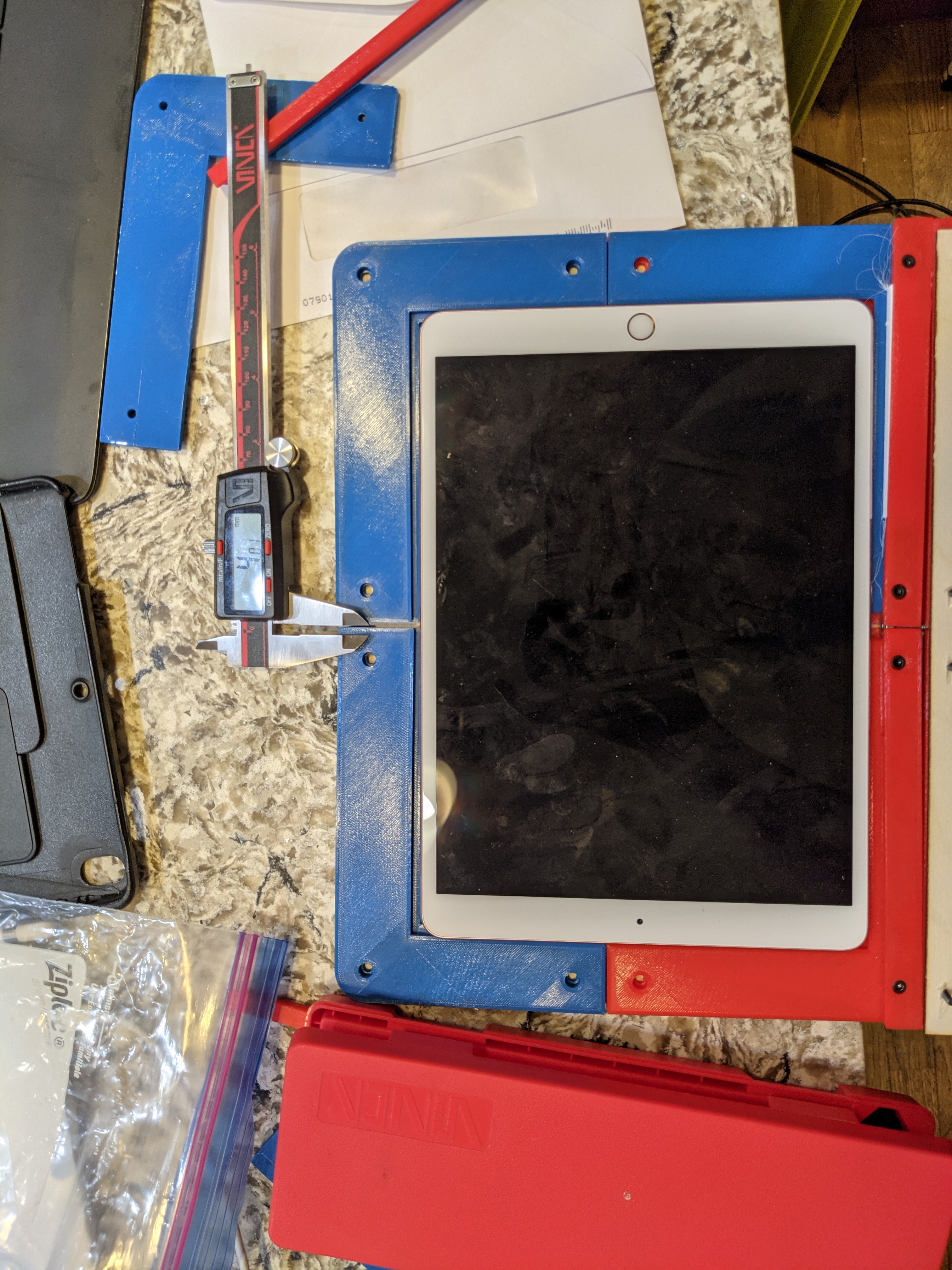
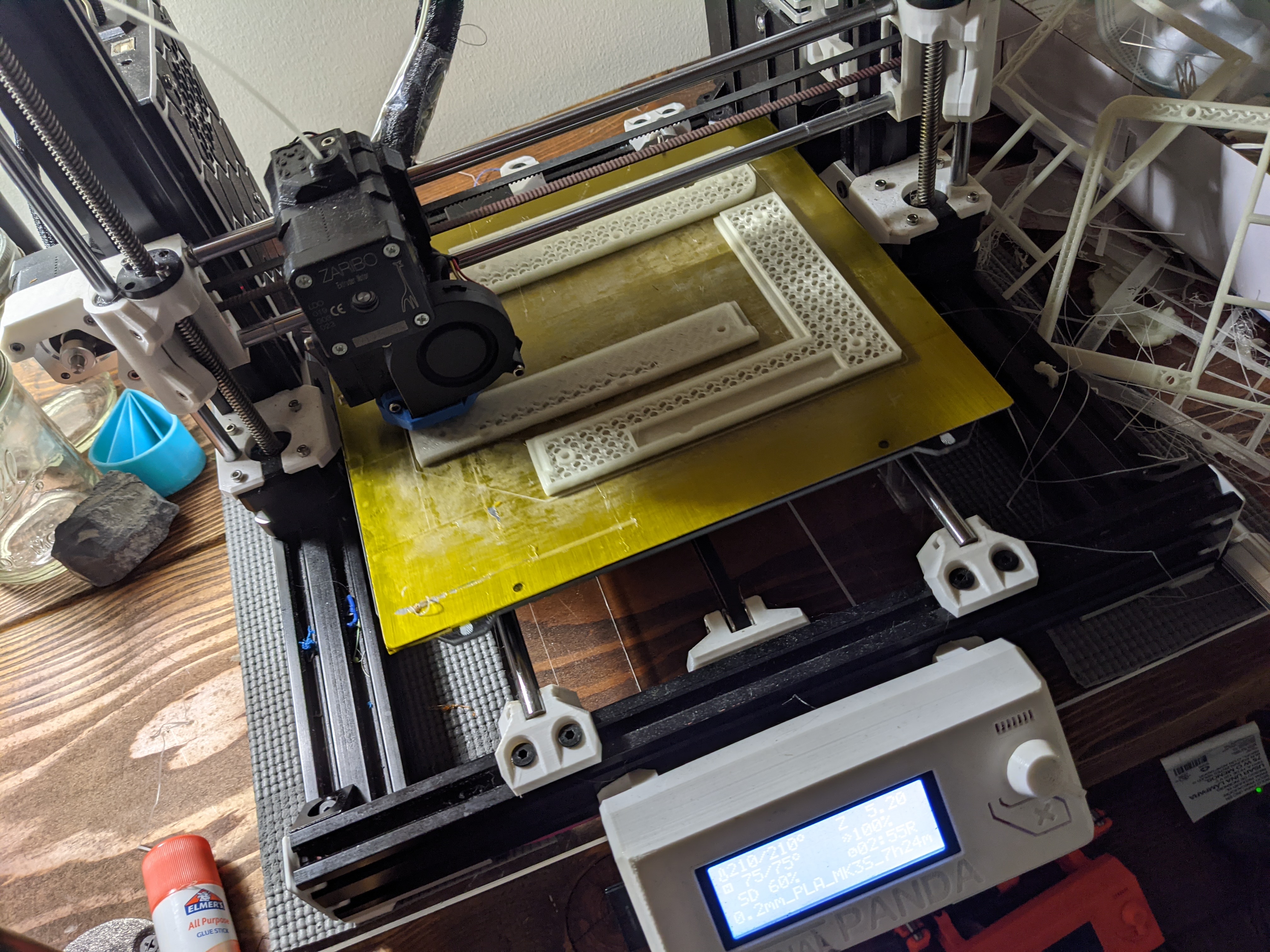
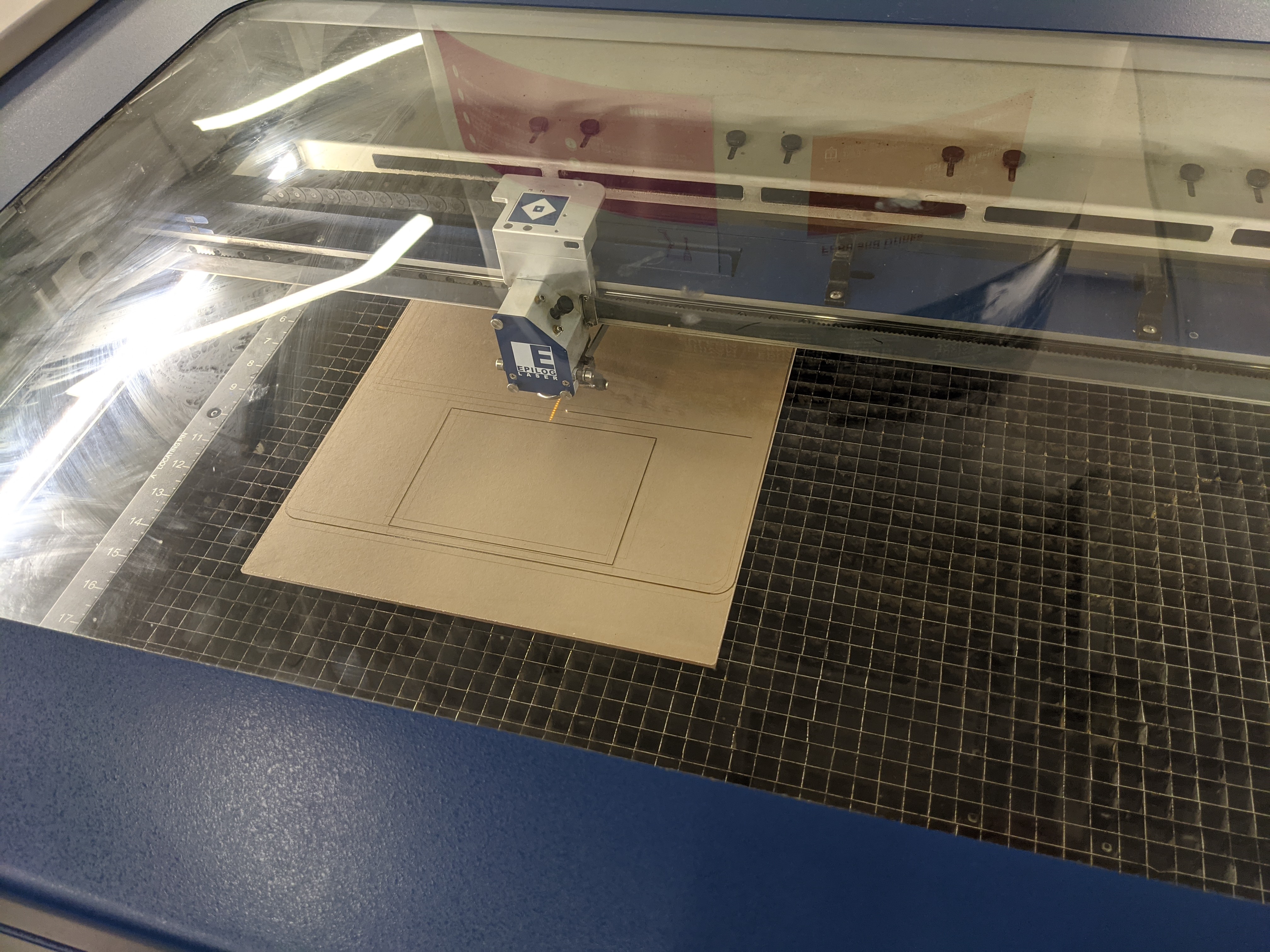
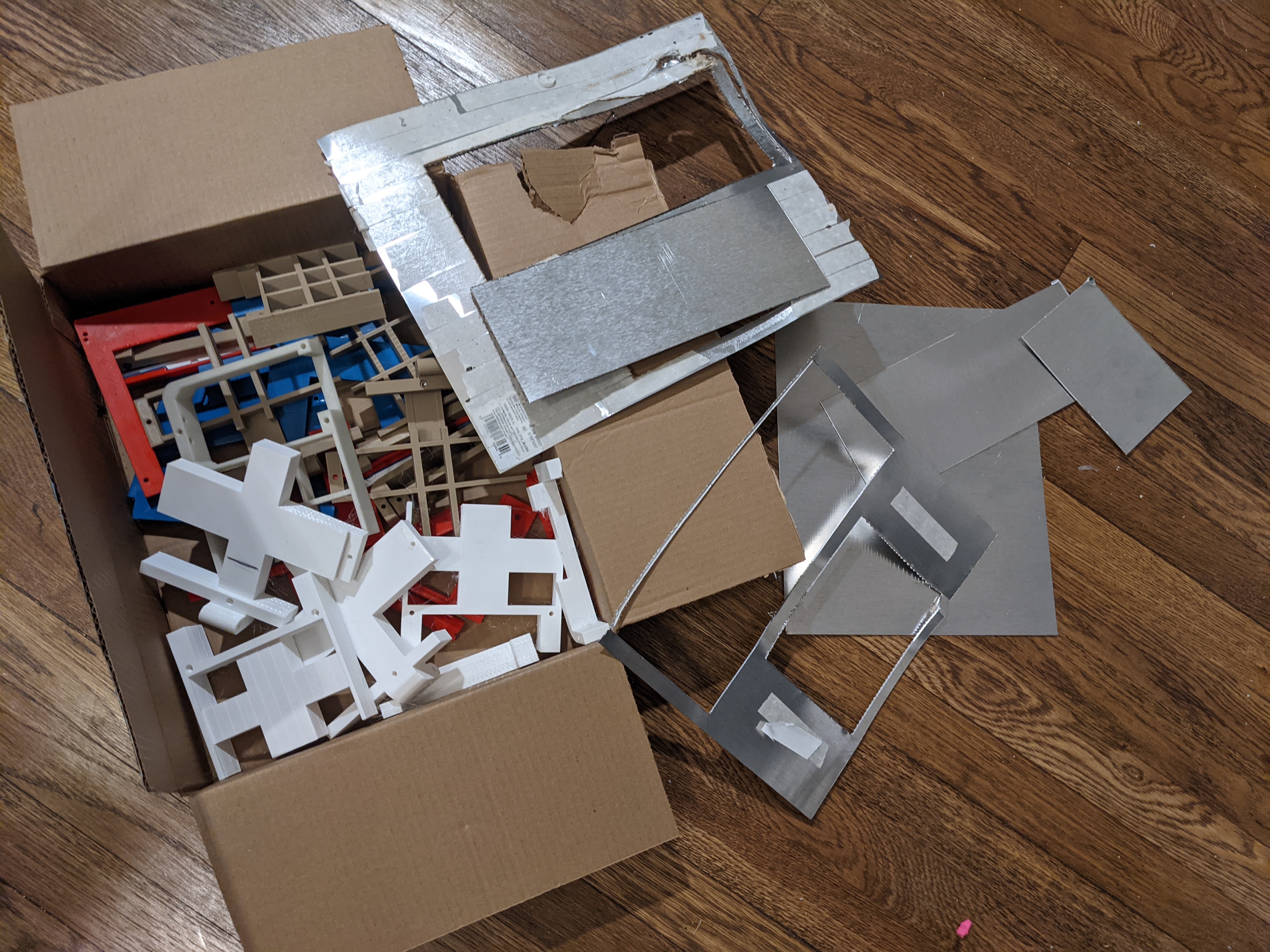
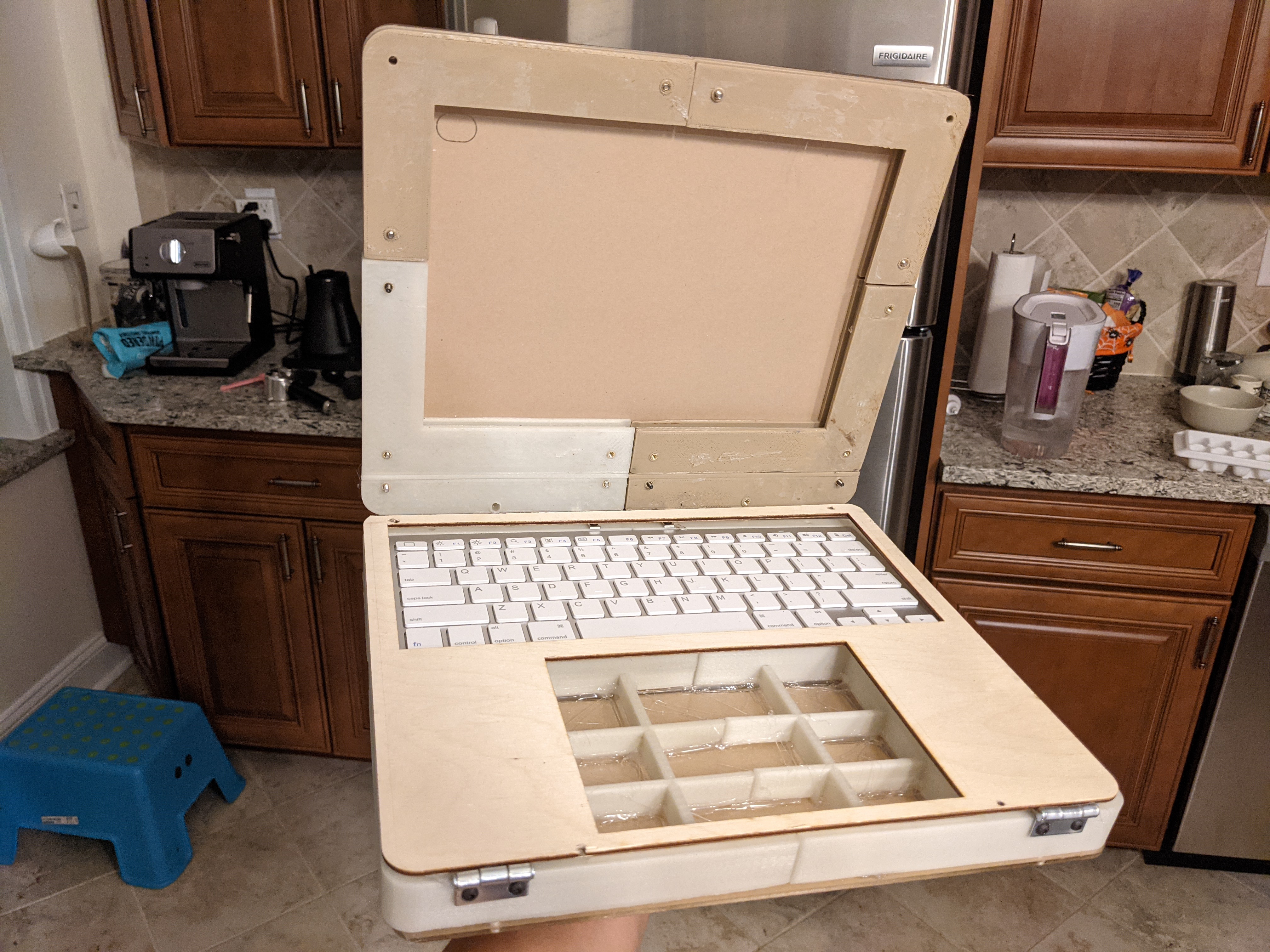
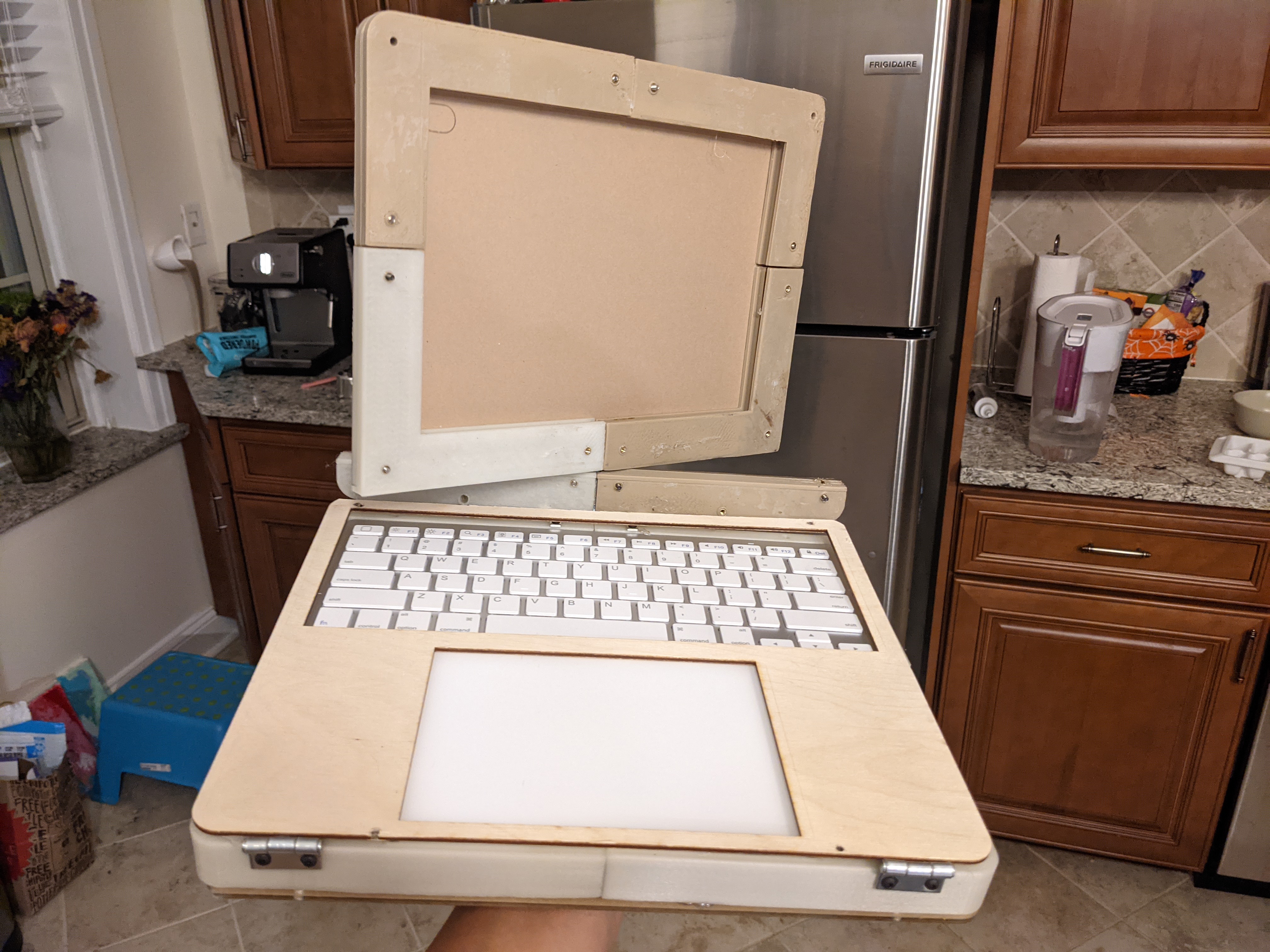
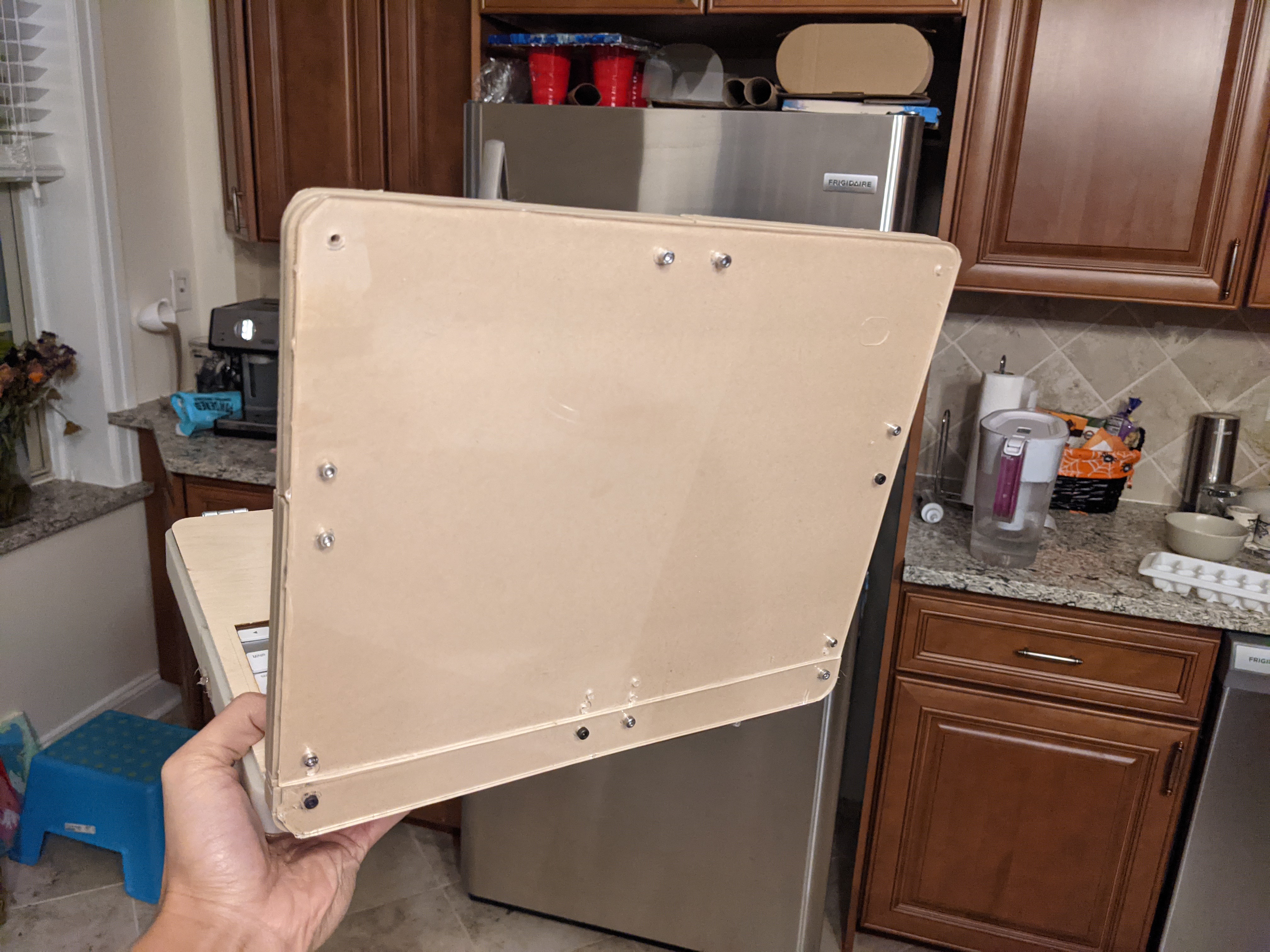
home
while (!deck.isInOrder()) {
print 'Iteration ' + i;
deck.shuffle();
i++;
}
print 'It took ' + i + ' iterations to sort the deck.';